Hydraulic filtration
Mobile | Industrial | Marine | Energy
Different types of hydraulic filtration
We supply the hydraulic filter you need for your hydraulic application.
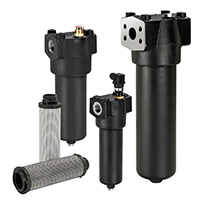
What are hydraulic filters and why you need them
Hydraulic filters are supplies that protect your hydraulic system components from damage due to contamination of oils or other hydraulic fluid in use caused by particles. Every minute, approximately one million particles larger than 1 micron (0.001 mm or 1 μm) enter a hydraulic system. These particles can cause damage to hydraulic system components because hydraulic oil is easily contaminated. Thus, maintaining a good hydraulic filtration system with the right supplies by DTA will increase the lifetime of a hydraulic component.
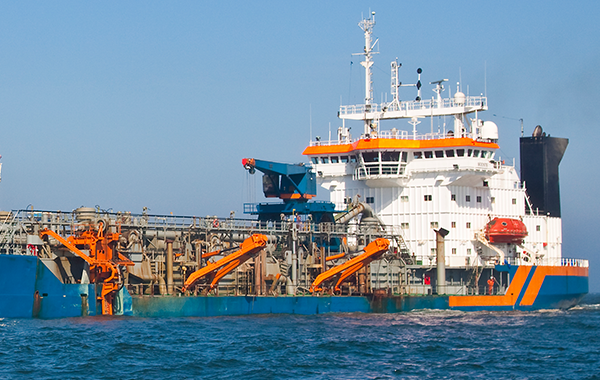
Hydraulic filters and supplies prevent particles from entering your system
The wear of hydraulic system components and hydraulic equipment is dependent on contamination, and the existence of metal parts in hydraulic system oil (iron and copper are particularly powerful catalysts) accelerates its degradation. Hydraulic filters help to remove these particles and clean the oil in your supplies on a continuous basis. The performance for all hydraulic filtration supplies is measured by its contamination removal efficiency, such as high dirt-holding capacities.
A hydraulic filtration system includes hydraulic filters to remove dirt and particles on a continuous basis
Hydraulic filters and other hydraulic filtration supplies from our company for hydraulics help to remove these particles and clean the oil on a continuous basis. Almost every hydraulic system contains more than one hydraulic filter. The hydraulic filters between pump and actuators are referred to as pressure filters and the hydraulic filters between the actuators and tanks are low pressure or return line filters.
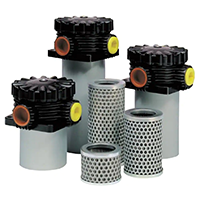
Low pressure filters
Low pressure filters operate at pressures of 10 bar or less. Suction filters are used for coarse filtration and return line filters or bypass filtration for fine filtration.
Type of low pressure filters
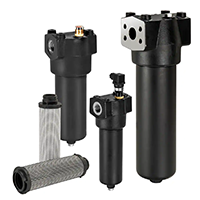
Heavy duty filtration
Heavy duty filtration for demanding hydraulic applications under tough conditions in continuous operation. It's flow rate is high at low to medium hydraulic system pressure.
Type of heavy duty filtration
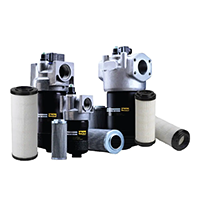
Standard pressure filters
Pressure line or standard hydraulic pressure filters are commonly used in a hydraulic system. It protects your hydraulic components against wear and tear.
Type of standard pressure filters
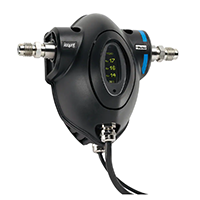
Contamination control
Contamination control is a very important element of a hydraulic filtration system. Changing filter elements on a regular basis prevents clogging and improves oil quality.
Type of contamination control
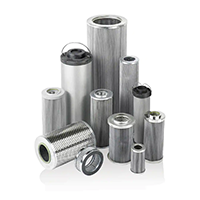
Par Fit replacement elements
With Par Fit you enjoy the benefits of a one-stop-shop solution for all your hydraulic filter elements of high quality at competitive prices and immediate availability.
Type of Par Fit replacement elements
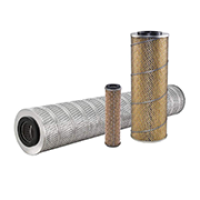
Reservoir equipment
Reservoir equipment includes components to prevent contamination as well as components to measure tank fluid level, temperature and pressure of the oil.
Type of reservoir equipment
Order your hydraulic filtration supplies with us
Whether you are looking for hydraulic filters or other supplies such as a pressure relief valve for your system, DTA has got you covered. In our assortment, you can find many market-leading brands of which we sell hydraulic filtration supplies, as well as spare parts. Are you looking for some advice before you order a part? Contact our team for expert advice.